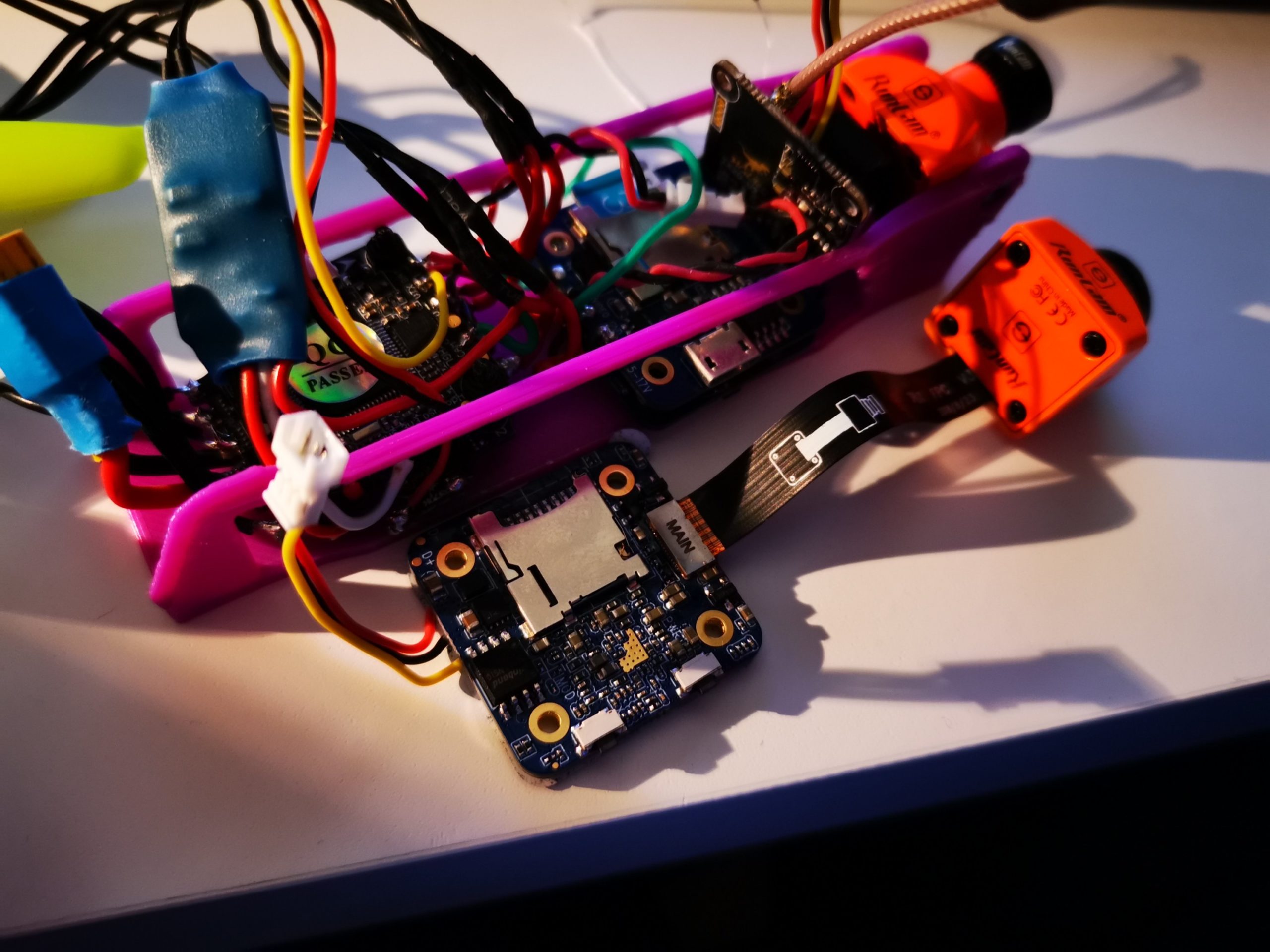
Getting more maintenance friendly
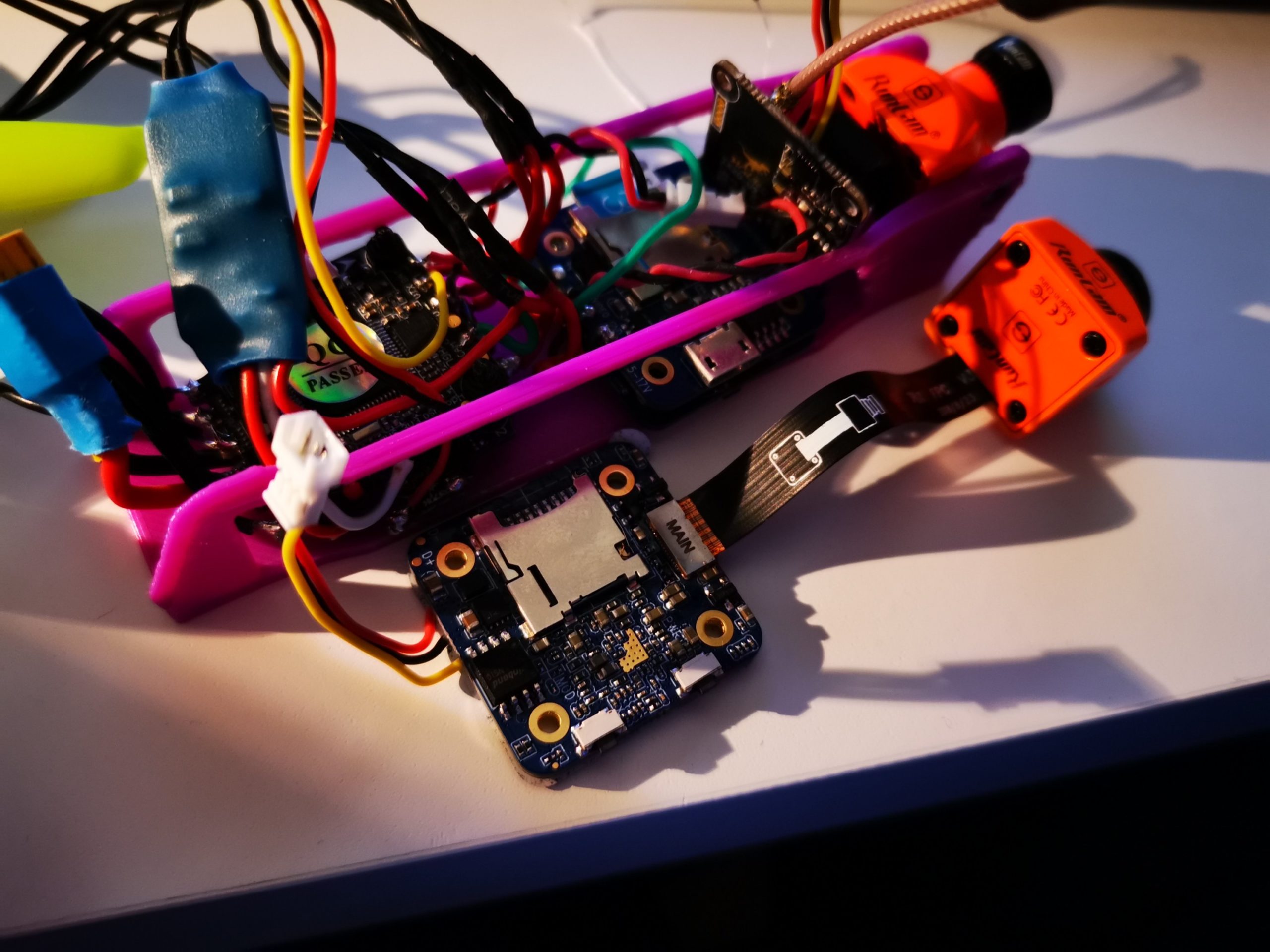
@ scheisser.net . . . . . . . . . .“If you always do what you’ve always done, you’ll always get what you’ve always got.” -Henry Ford
As I got my first feedback on thingiverse I want to inform everybody to be careful when you put the upper case over the external ports as this is the most fragile part. Designwise I didn´t found a workaround for this area as result it can happen if you push too much that the connections between the ports break off but with a liztle bit patience you can set iz in place as one piece.
As I accidentially deleted last week all config files from the SD.card of my tinyfabbed Tiertime Cetus printer I took some Corona time the last few days to rebuild all config files for the upgraded Cetus printer. I use the heatbed with external controller board plus the tiertime CPU plus the tiertime TFT on a MK2 Cetus. It is mandatory to upgrade to physical endswitches!!!
find HERE a package with a working cetus setup file plus mypanel config and the mandatory cura (4.5) printer config. Hope that helps anybody out there.
due to the fact Germany is in a kind of lock down I took some time to work again on the fully printable frame design.
This is one of the less options available to pack the needed modules in an ultra tiny 135mm formfactor. there is not much space left and this is not a final stage but could be a base for the next prototype. I will see…
You are looking for the holy milkcow? Maybe the following is something for you…
I´m working on this design since early 2018. 3D printing offers a lot of new ways to design things but brings a lot of challenges, too. I´m in the lucky situation to have access to a capable 3D printer and a lot of different filament materials to play around.
The design I came up with is different than any others, but I have to admit that there are more and more similar designs popping up. That´s why I decided to start a new mockup here. This will be the successor of my super135 design posted earlier @ rotorbuilds. There are a lot of open questions to move the super135 to a fully printable frame. Nobody wants to mess around with vibration issues, flimsy designs, props or frameparts in the view of the recording cam, battery under the frame, short flight times and the FAA or similar/other local regulations.
This is not a x-style or h-style frame and even in the same weight limit as a cinewhoop it stands out with the possibilities – this is something different and sets a new category . Same is applicable for the earlier introduced super135 but this one needs carbon and a CNC mill. This is a redesign of the super135 which has also an outer „teardrop“-frame to provide as much safety to the internals and motors as possible in case of crashes. A crash in this category can cause a huge destruction derby for the internal components as well as for the batteries. I´m trying constantly to get the best out of the tech and optimize my designs to make it more durable, stiff and offer more options and safety.
Hope you enjoy and let´s the discussion begin.